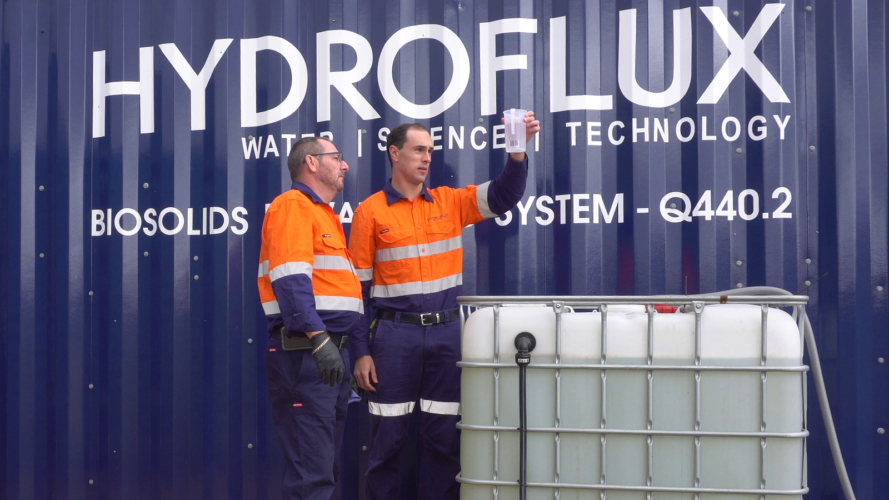
Sustainable Savings: How Optimising Your Chemical Treatment Plant Can Cut Costs
August 8, 2023
When operating a physical chemical treatment plant such as a DAF or clarifier, the performance of the plant is highly dependent on the chemical program used and the respective dose rates and generally speaking, the more chemicals you add, the better the treated water quality is.
Whether the physical chemical treatment system is discharging water to sewer or further treatment processes onsite, it is quite common to find that the physical chemical treatment system is configured to produce a treated water quality far in excess of what is actually required, and whilst it may be aesthetically pleasing to have clear and colourless water discharging from this physical chemical treatment plant, it is quite probable that the way the system is operated is not so attractive to the bottom line.
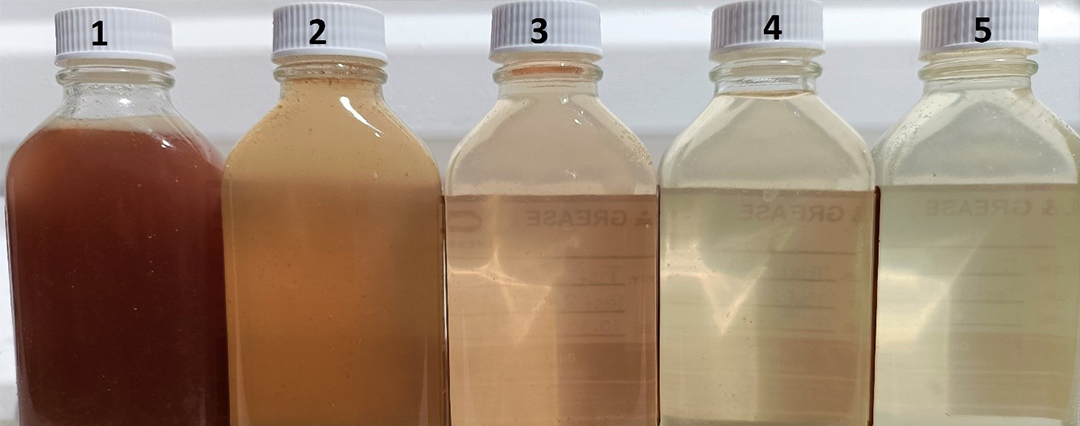
What you can do
There are many variables in play when operating a chemically assisted primary treatment plant, so the first step is to identify what those variables are. We will use a wastewater treatment plant discharging to the trade waste as an example to put this in perspective.
If a water authority charges $1.00 per kg for total suspended solids (TSS), and your DAF system is consistently producing good quality water at 100 mg/L TSS, then with a flow rate of 1 ML/day, your TSS daily mass charge will be $100/day. This is a simple linear equation, so if your DAF was not performing as well and producing a discharge at say 500 mg/L, this mass discharge cost will increase to $500/day (assuming that 500 mg/L in not in breach of any trade waste agreement.
Although this increase in cost may seem considerable, in order to achieve the lower $100/day cost, you would normally need to be dosing more chemicals, and this in turn will generate more sludge. It is often found that the costs for additional chemicals and sludge disposal are higher than lowering the chemical dose rate and paying a little extra for the additional TSS mass discharge.
The chart below is an example of a performance vs chemical cost assessment on a DAF system conducted by Hydroflux Utilities at a food processing plant. The customer was originally getting 95% TSS removal at a chemical spend of about $0.50/kL. When the chemical dose was reduced, the chemical spend went to $0.30/kL and the TSS removal decreased from 95% to 75% removal. While more TSS was discharged, the TSS concentration (and mass) were still below the agreed limit, and the mass cost for TSS only increased marginally – the outcome was a lower cost to operate.
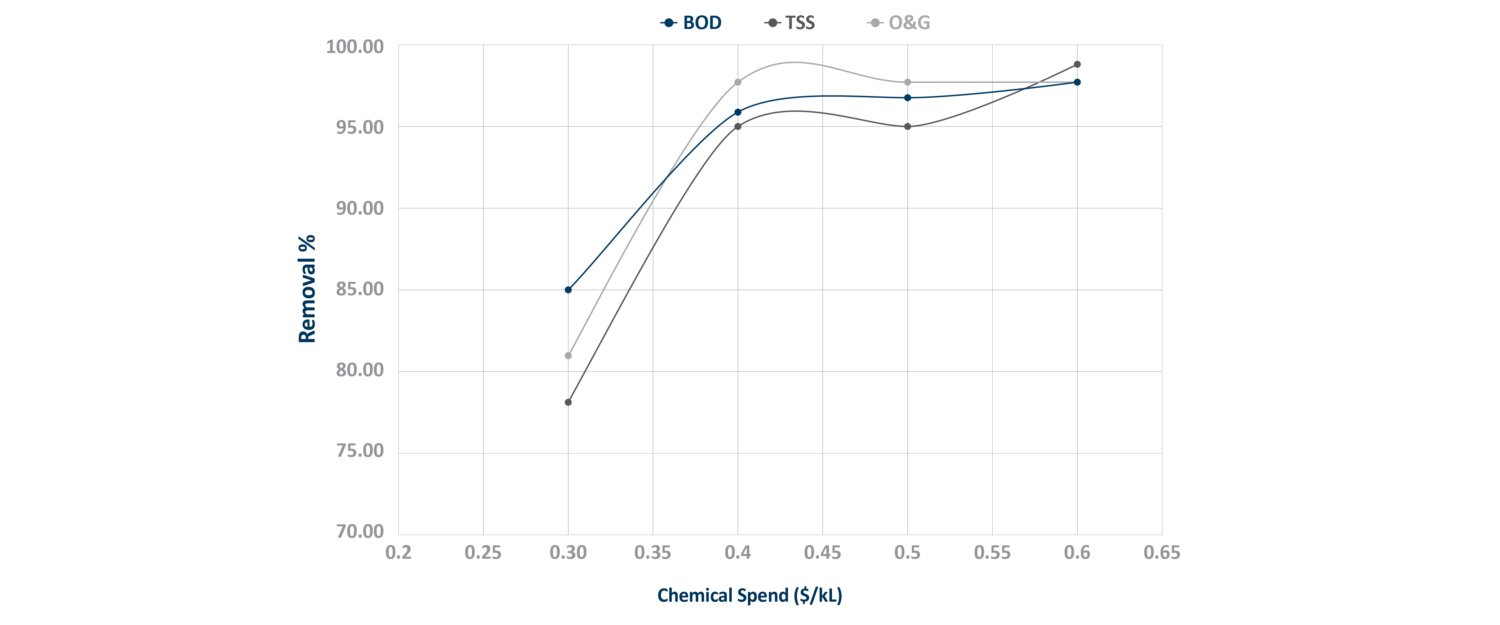
In this basic example alone, there are multiple variables including the actual chemical program used and the amount of sludge it generates, the cost of the chemicals, delivery methods, the dry solids concentration of the sludge, chemical costs of conditioning sludge, sludge classification and disposal cost to name just a few. If we considered an example whereby the wastewater is discharge to an onsite secondary treatment plant, then power consumption and waste activated sludge volumes also come into play.
Engaging Hydroflux Utilities to conduct a wastewater treatment plant optimisation study can reduce the operating costs of your wastewater treatment plant. We have the process knowledge, skills, specialty chemicals and a national presence to provide this service to any type of business operating a physical chemical wastewater treatment plant.
For more information click here
About the Hydroflux Group
The Hydroflux Group aims to deliver the highest level of engineering and scientific know-how to the emerging issues of sustainability, climate adaptation and environmental protection with a specific focus on water and wastewater.
As part of its vision and mission, Hydroflux has always taken its climate responsibility seriously. In 2022, Hydroflux became Australia’s first water treatment and technology company to achieve Climate Active carbon neutral certification for its organisation and products. It knows that partnering with customers and clients is the most significant impact it can have in its journey.
The Group employs over 100 staff and operates throughout Australia, New Zealand and the Pacific Islands, with office locations in Sydney, Melbourne, Brisbane, Perth, Auckland, Suva and Portsmouth.
Up Next
Categories
- Tradeshows
- Climate
- Community Engagement
- Corporate Announcements
- Group News
- Newsletters
- Product News
- Project Announcement